Per assistere l’aggiornamento di un impianto, una delle più grandi raffinerie d’Europa ha scelto e presentato a SPIG una sfida audace: lo smontaggio e il rimontaggio completo di una torre di raffreddamento (CT) SPIG in polimeri caricati con fibra, comprendente due celle, in un lasso di tempo ristretto di 21 giorni, per sincronizzarsi con una fermata programmata.
Il team di SPIG ha progettato il piano di esecuzione che richiedeva velocità e precisione.
La costruzione della CT a due celle è iniziata in un’area dedicata, accanto alla torre originale che è rimasta ferma durante il progetto. La nuova torre misurava 12×24m2 e raggiungeva un’altezza di 14 m.
SPIG ha preassemblato il 90% della torre di raffreddamento fuori dal bacino prima di posizionarla al posto del vecchio sistema di raffreddamento. Il team di costruzione ha costruito una struttura metallica intorno al tetto della nuova torre per migliorare la stabilità e facilitare il successivo sollevamento con la gru.
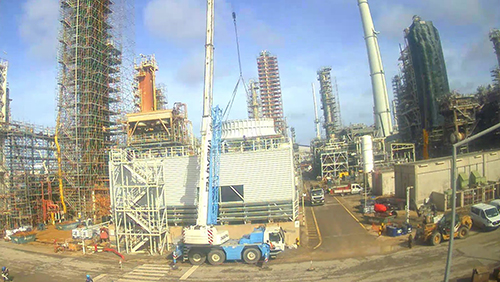
Il progetto è stato rispettato nonostante le condizioni meteorologiche avverse. Era fondamentale arrivare al giorno del sollevamento con tutti i lavori di demolizione completati. Avendo assemblato completamente la torre all’aperto, era essenziale attenersi rigorosamente a tutte le tolleranze specificate nei disegni di assemblaggio per evitare problemi con i pilastri di supporto. Molti compiti dovevano essere attentamente sequenziati e pianificati, compreso il collegamento della flangia della colonna montante del cliente alla nuova testata.
Con il proseguire del conto alla rovescia di 21 giorni, l’attenzione è passata dalla costruzione allo smantellamento della torre in legno esistente. I giorni sono stati dedicati allo smontaggio della torre di raffreddamento in legno esistente e alla preparazione del terreno per l’installazione del nuovo sistema di raffreddamento.
A pochi giorni dalla fine, gli ingegneri della SPIG sono passati senza problemi dalla decostruzione all’assemblaggio e al sollevamento del nuovo CT. Con un peso di 30 tonnellate, il nuovo CT è stato issato in posizione su pilastri alti 3,5 metri. I componenti finali da installare comprendevano pile di ventilatori preassemblate, gruppi meccanici preassemblati e la scala.
La procedura di installazione unica ideata dagli ingegneri della SPIG non solo ha raggiunto i suoi obiettivi, ma ha anche comportato un risparmio di tempo del 50% rispetto alla pratica standard di smontare il vecchio CT e successivamente assemblare i nuovi componenti per montare l’intero CT in posizione subito dopo lo smontaggio. Questa efficienza sottolinea l’efficacia del nostro approccio su misura, che consente di rispettare le scadenze più rigorose senza compromettere la precisione.
Questo progetto, che ha richiesto competenza, attenzione ai dettagli, innovazione e lavoro di squadra, è stato completato nei tempi previsti e ha rispettato tutte le misure di sicurezza, garantendo un’esecuzione sicura e conforme all’intero processo.
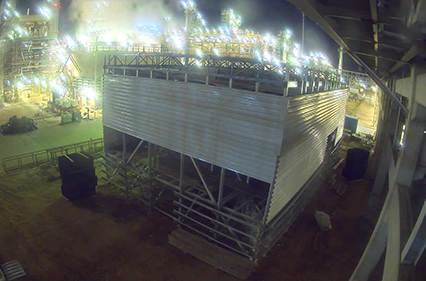